Six Sigma Consulting
We utilize the Six Sigma Methodology to help your organization improve both quality and efficiency.
Approach & Key Highlights
Our Six Sigma methodology is designed to drive improvement with precision. We begin by working closely with your team to understand the problem areas and identify available data. Then, we analyze the data and engage with subject matter experts to uncover the meaning behind the numbers.
Each Six Sigma project is customized to address your unique challenges, with results delivered quickly and effectively.
Every action is driven by data and aimed at achieving measurable improvements in quality and operations.
We turn data into actionable strategies through analysis and team collaboration.
Our Strategy
Efficient Solutions for Tangible Results
At Dynamic Insight Solutions, we take a practical approach to Six Sigma consulting, focusing on real-world results rather than theory. Led by Mark H. Murphy, a Six Sigma Black Belt, our consulting service is built on a foundation of quality, efficiency, and data-driven decision-making.
Focused & Efficient Implementation
Our Six Sigma consulting follows a straightforward yet powerful process that maximizes impact while maintaining efficiency. By first identifying the core issues and existing data, we align on attainable goals and begin implementing targeted improvements.
The process is designed for flexibility, each project can stand alone or be part of a broader, ongoing improvement strategy, depending on your needs. With a strong emphasis on actionable results, we ensure that your organization can continuously evolve.
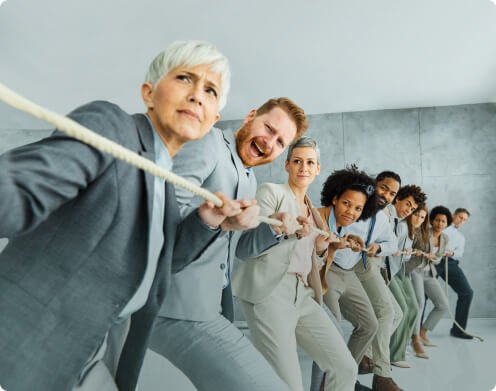
frequently asked questions
Get the Answers You Need for Effective Healthcare Operations
How does Six Sigma benefit my organization?
Six Sigma can help you increase efficiency, quality, and employee buy-in. Six Sigma methodologies help identify waste and failure points to improve your operation. When you do Six Sigma with DISC, we involve your people in a controlled decision-making process. This develops ownership and buy-in with your staff.
How long does a typical Six Sigma project take?
The times vary depending on the size and scope of your performance or quality improvement project. A small project with identified and readily available data could take as little as four hours of staff meeting time, two hours of implementation oversight (your staff or ours), and four hours of DISC time behind the scenes.
Large performance and quality improvement projects on complicated systems can last for extended periods of time. DISC will conduct large portions of the data and systems analysis behind the scenes to reduce the time burden on your staff. We can also provide data capture and auditing services to free up your staff to continue operations. Almost all of the work conducting final analyses of data, solution development, work plan development, and outcome review takes place in our consultant led Performance Improvement Teams. (Your staff members are the team.) Typically, these meetings can last from two to four hours in the beginning. Longer projects may eventually drop to about an hour once you are monitoring and tweaking operations. The space between meetings will depend on your project’s cycle time and implementation speed.
Can Six Sigma consulting be applied to my existing operations?
Yes. Six Sigma is almost always applied to existing operations. It can also be applied as part of the design for a new operation.
What if my company does not like the proposed solutions?
Your company’s representatives ultimately decide the solutions generated within the Six Sigma process. DISC recommends that a person or persons with the authority to make the decisions under consideration serve as a Project Lead(s). We further recommend that the person supervising the Project Lead(s) participates as the Project Champion. They do not attend all the meetings but review all the notes and meet with the Consultants and Project Leads. During these meetings, they provide feedback, offer guidance, and clearly state any non-negotiable issues.
BLOG
Insights & Resources
Correctional Nurse Retention Correctional healthcare environments are among the most demanding in the medical
When run correctly, Pharmacy and Therapeutics meetings are one of the most important parts
Riding the Churn: Thriving in the Era of DOGE “The Churn was just what
Emotional Freedom Technique (EFT) combines acupressure, somatic therapy, and cognitive techniques to offer a
Sleep is a fundamental pillar of health, affecting cognitive function, mood, and overall well-being.
Understanding Anxiety: The Cycle of Worry Anxiety is a complex issue, often fueled by
Get In Touch
Reach Out for Expert Guidance
14361 Sommerville Ct Midlothian, VA 23113
markhmurphy@dynamicinsightsolutions.com
Phone : +1 804-406-9186